Tools for Prototyping Physical Products
After defining the purpose and setting the attributes of your prototype, you are ready to pick the right prototyping tool. Have a look at our list of tools we typically use for prototyping physical products.
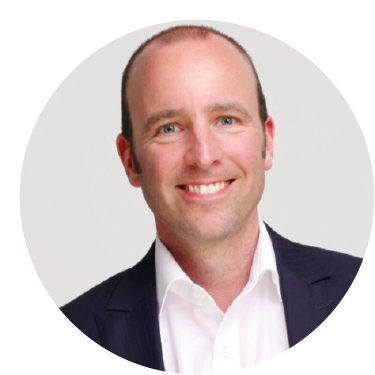
Kai Dierkesmann
Business Design Coach
Content
1. Example Tools
We have been using the following tools to design and build prototypes of products in Business Design projects:
Tool | Comment |
Pen & paper | A good tool to get started - even if you are untalented |
Hard foam | Great material which can be worked on with hot wire cutter, knifes, sanding paper and rasps |
Makedo | Flexible plug-in system to realize mechanical structures with different materials |
MakerBeam | Aluminium profile system to build racks, structures etc. for prototyping with only few steps |
Dremel 4000 | Very powerful multi-functional tool for sanding, cutting, drilling and milling |
FimoAir | Air-curing modeling material for all who prefer modeling with their hands instead of CAD |
Apoxie Sculpt | Air-curing epoxy for quick modeling of 3D shapes |
InstaMorph | Easy to use modeling plastic. Simply a great material... |
Fantastic Plastic | Plastic pellets which can be molded by hand |
CURBELL Plastics | Manufacturer of different materials for plastic modelling |
Form card | A special “bio-plastic” in credit card size which can be molded by hand after warming |
Modulor | Online store with a great offer of all sorts of material for design and prototyping (e.g. foam materials) |
MakerBot | Simple desktop 3D-Printer |
Creality CR-10s | 3D printer with a printable format of max. 30x30x40 cm |
Ultimaker | Similar to MakerBot, but a bit easier to operate |
Fab@Home | Open-source project with kits for 3D-printers |
FabLab | High-tech workshop in many cities in Germany e.g. Munich |
Cura | In oder to 3D-print a CAD file it needs to be sliced into the single layers. Cura is freeware which does exactly that. |
CNC Raptor | Affordable CNC-milling |
Epilog Lasercutter | Great tools to cut 2D shapes out of different materials (Zing series) |
Craft Robo | Affordable cutting plotter for paper, cardboard and vinyl |
Autodesk 123D | Easy to handle and free 3D modeling software, similar to SKetchUP |
Google SketchUp | Very easy to learn 3D modeling software |
Autodesk 123D Make | Realize 3D models with simple 2D parts (DIY) |
Autodesk 123D Catch | Mobile app which generates CAD files from 3D shapes |
Rhino3D | …for CAD pros |
FreeCAD | A full scale parametric CAD software (freeware) to design very accurate components. Easy to learn for immediate success. |
BoxShot | 3D rendering software to fake product packagings, handbooks and more for the quick marketing flyer |
Blender | Very powerful and versatile 3D design tool for all sorts of shapes (parametric, organic). Included is a powerful rendering machine to create photorealistic surfaces of 3D models. Needs certain expertise to work with. |
Photoshop | ...for design pros |
Origami | Plugin for Adobe Illustrator to develop and print Origami cuts |
Phidgets | Modular system for developing electronic control and regulation systems even without studying electrical engineering |
Open-source platform with several very good communities for developing simple hardware and software systems (sensors, actuators, WiFi, Bluetooth, GSM). Nearly unlimited opportunities, but needs some skill in coding. | |
Tessel.io | Beautifully integrated IoT developer kit to connect up to two sensors per plug-in board. No hardware knowledge is required! |
The "iPhone" for IoT projects for collecting data from a variety of sensors according to the Plug&P(l)ay principle | |
Middleware components for the rapid development of IoT solutions | |
Pinguino | Similar to Arduino with its own IDE development environment |
A credit card-sized mini-computer that can easily access and connect displays, Internet services, etc | |
BeagleBoard | Linux computer with the size of a credit card |
NEOPIXELS | ...another linux computer with the size of a credit card |
Prototyping Interfaces | Platform for the development of interactive electronic prototypes |
and much more | This list is far from complete and is just a short summary with a focus on look & feel prototypes. Make up your own mind and use a tool which fits your need. |
2. Example Usage
Hard foam, hot wire cutter & rasp
A fast and easy way to build a look & feel prototype is to cut 3D shapes out of hard foam based on a drawing of the product. Hard foam is a good choice because it has a higher density than usual white EPS / styrofoam and is therefore suitable for more precise shapes. Hard foam is more costly but also much stronger and more durable. A hot wire cutter is the best tool to cut the outlines of shapes. Templates or guides can be used to realize curved or straight cuts. A simple rasp (usually used for wood work) helps to quickly give solids an individual shape with many curves. Finally, sanding paper in different grains (60 - 400) gives it a smooth surface. In case the shaped solid shall be given a colored surface, acrylic paint is suitable. A prototype as of a joystick as shown here can be realized within 1 hour and an additional hour for painting & paint drying.
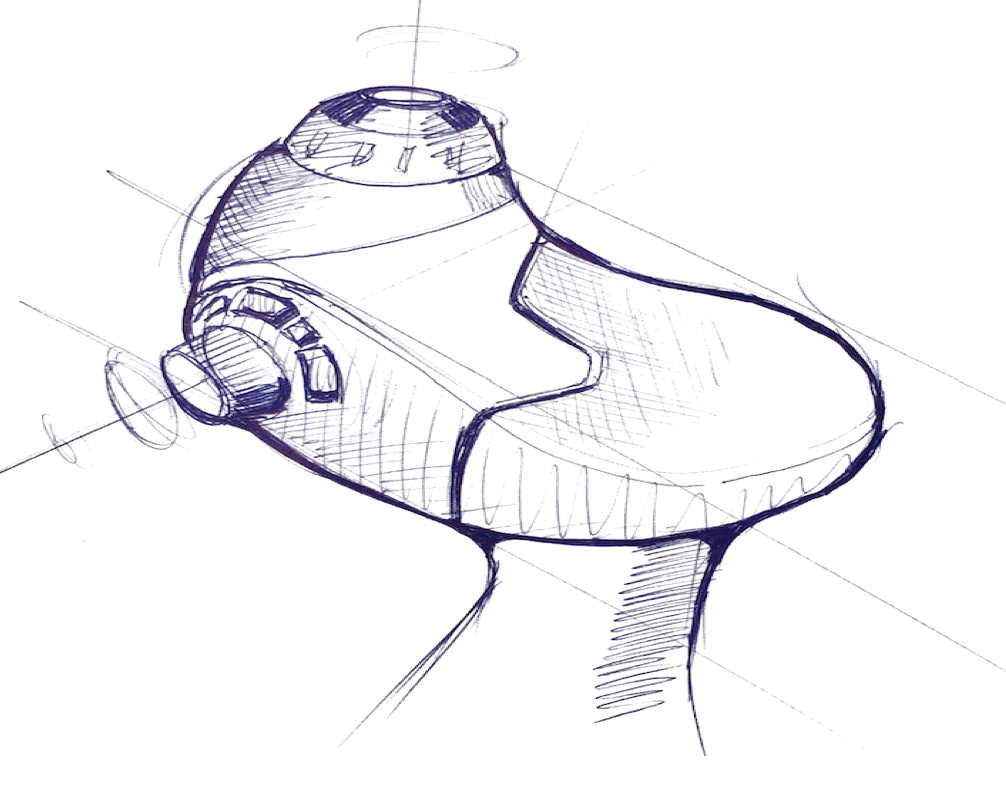
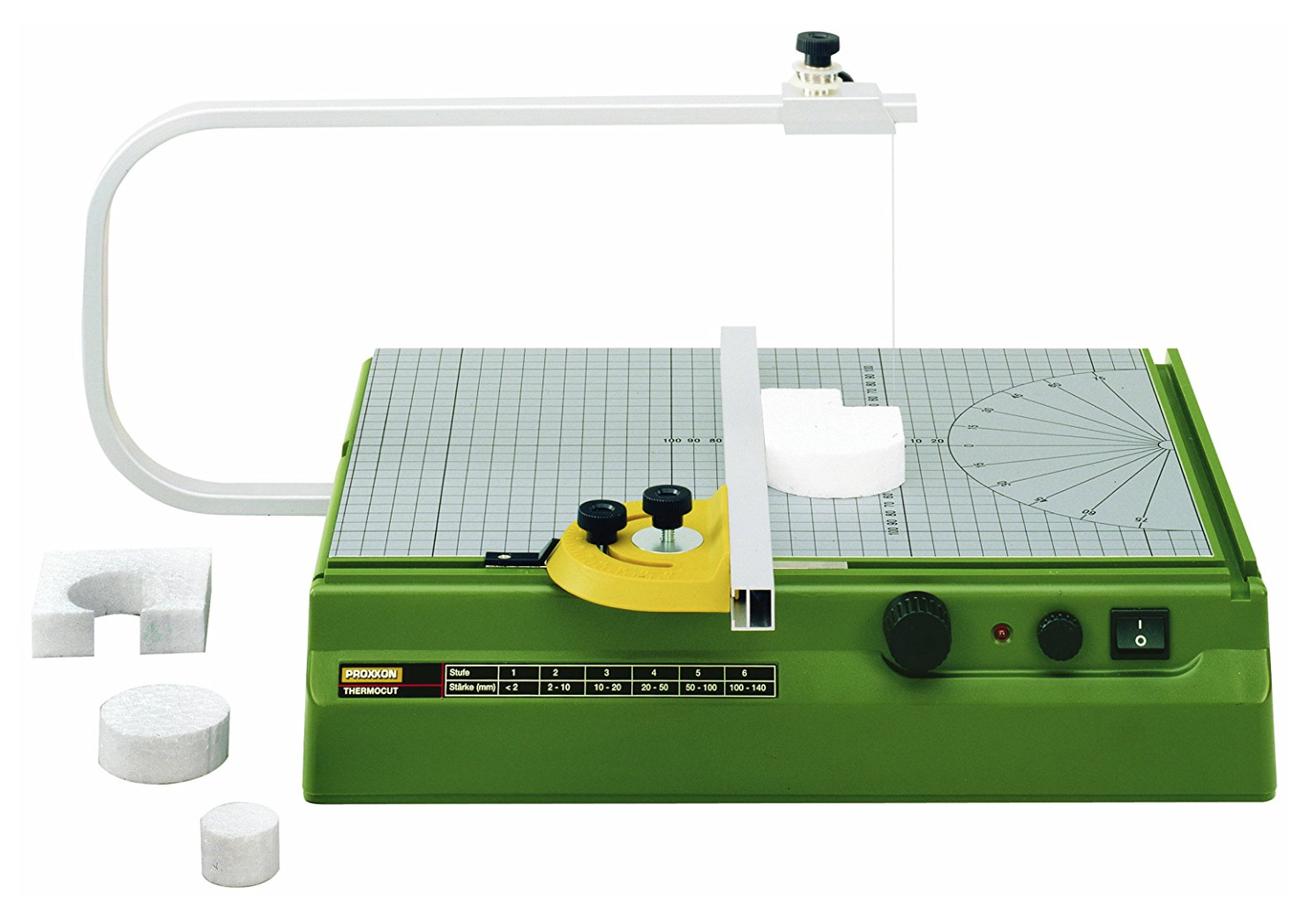
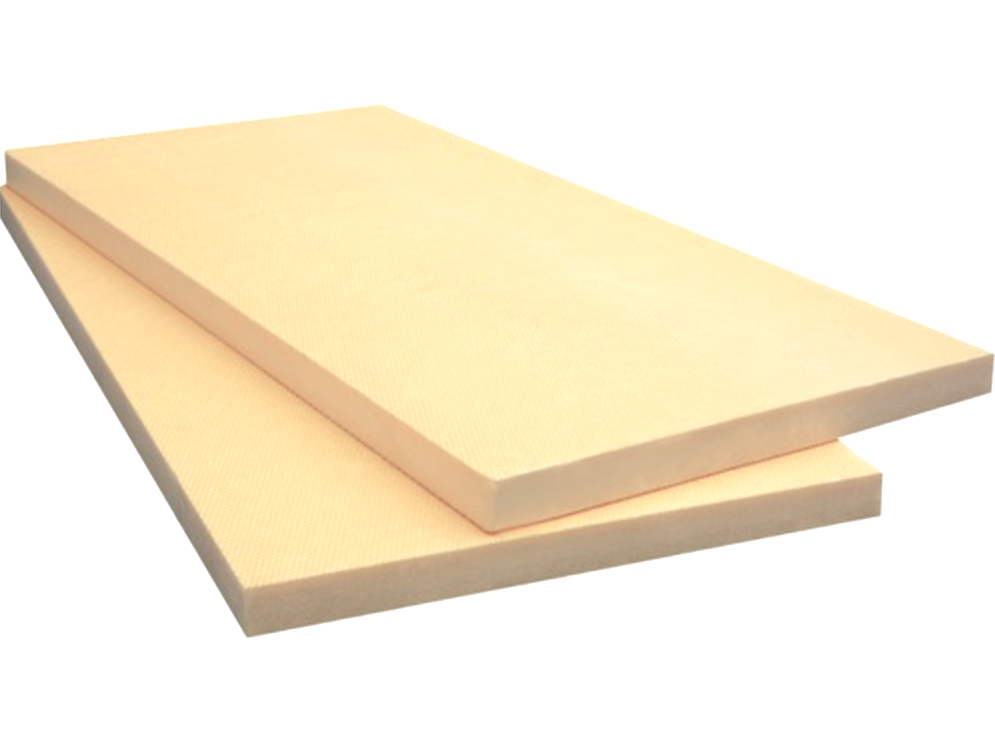
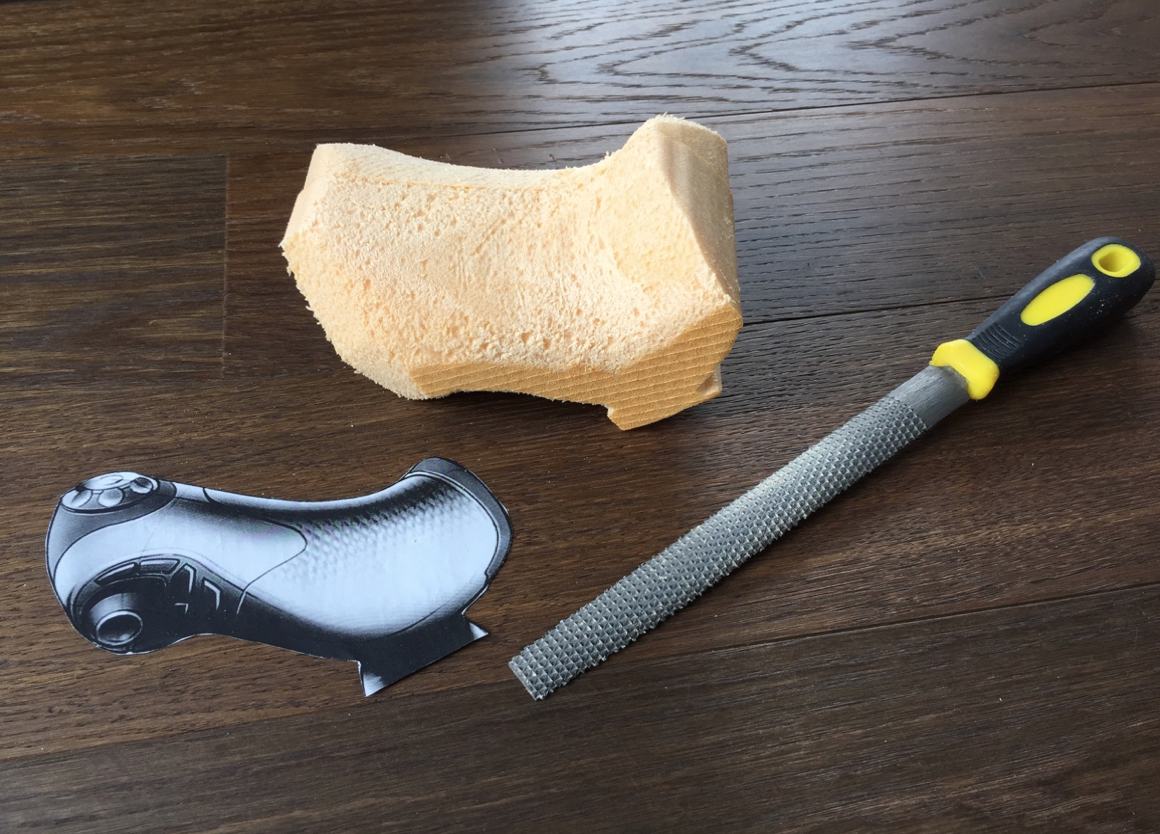
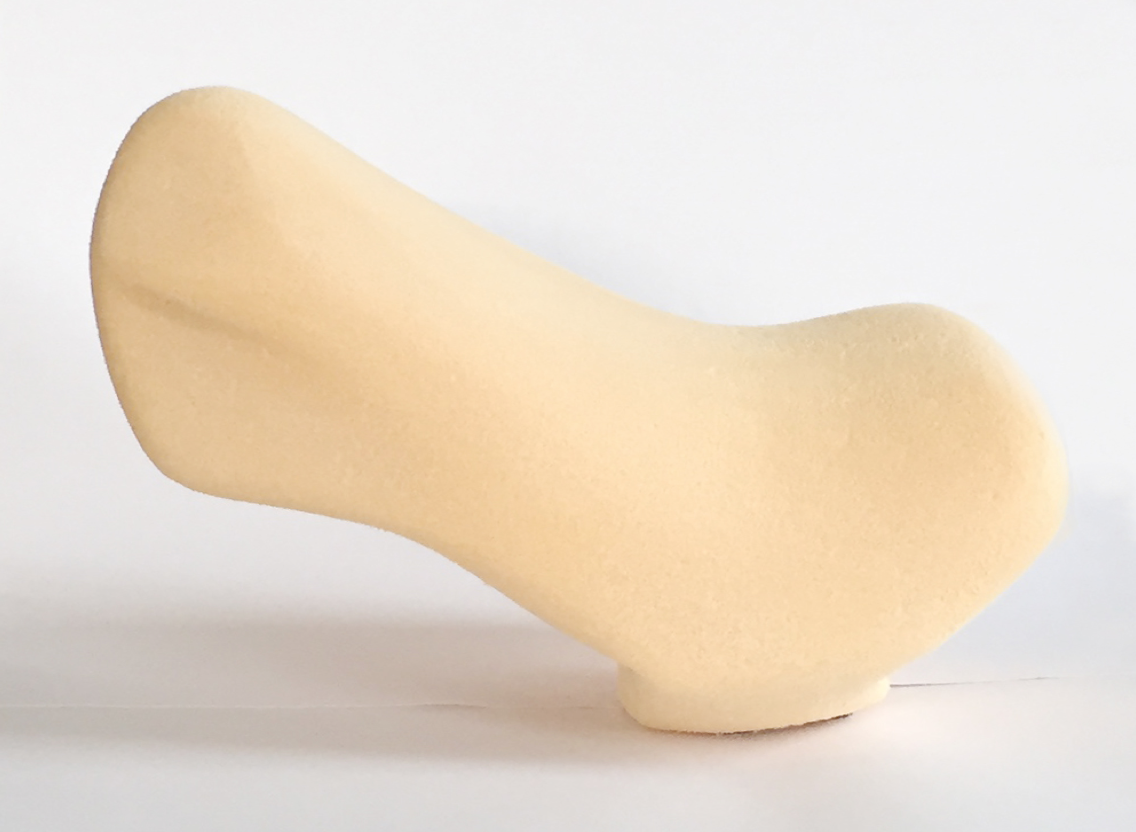
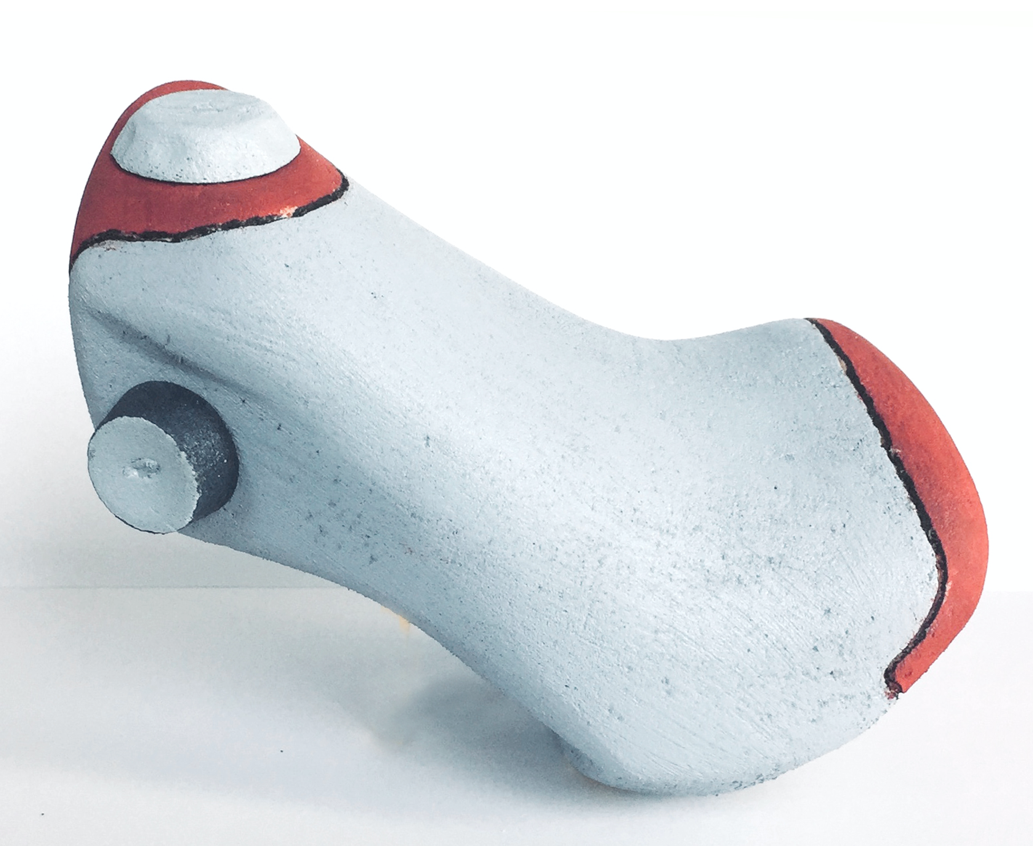
FreeCAD, Cura & Creality CR-10s
Building a simplistic CAD model e.g with FreeCAD enables a high degree of adaptability. Especially volumetric proportions can be easily shown and modified within seconds. Based on that, you can create a 3D-printed prototypes made of plastic materials such as PLA or ABS. Cura helps you to translate your FreeCAD model into slices that can be sprinted by a 3D printer like Creality SR-10s. If needed, you can glue 3D printed parts together (2k epoxy or many other glues), smooth edges with an electric drill or the surface with sanding paper (in different grains 60 - 400). In case you want to achieve serial-production-like surfaces, you can use 2k filler and a lot of sanding paper as a first step and finish with one or several primer coats, color coats and clear coats as a second step.
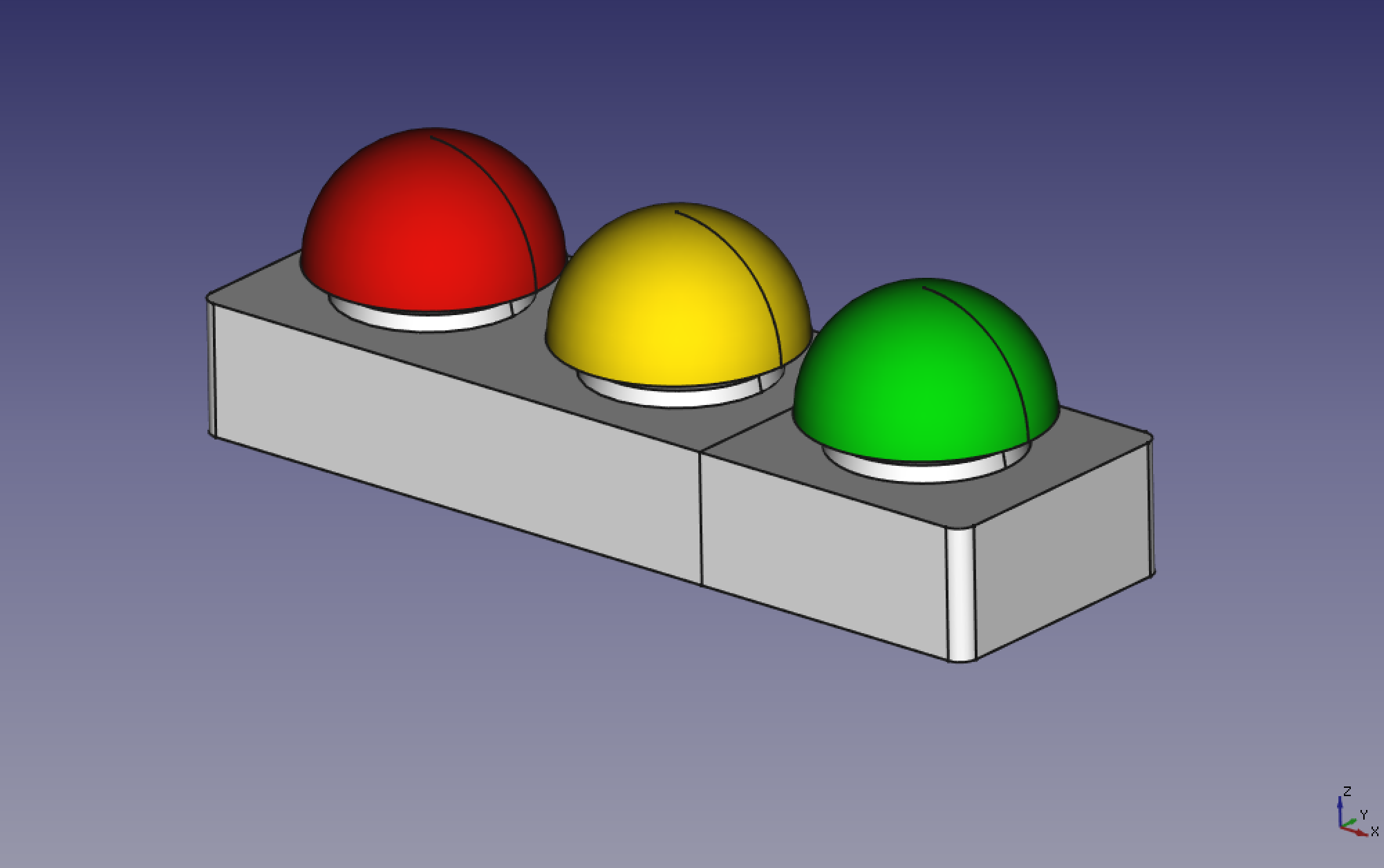
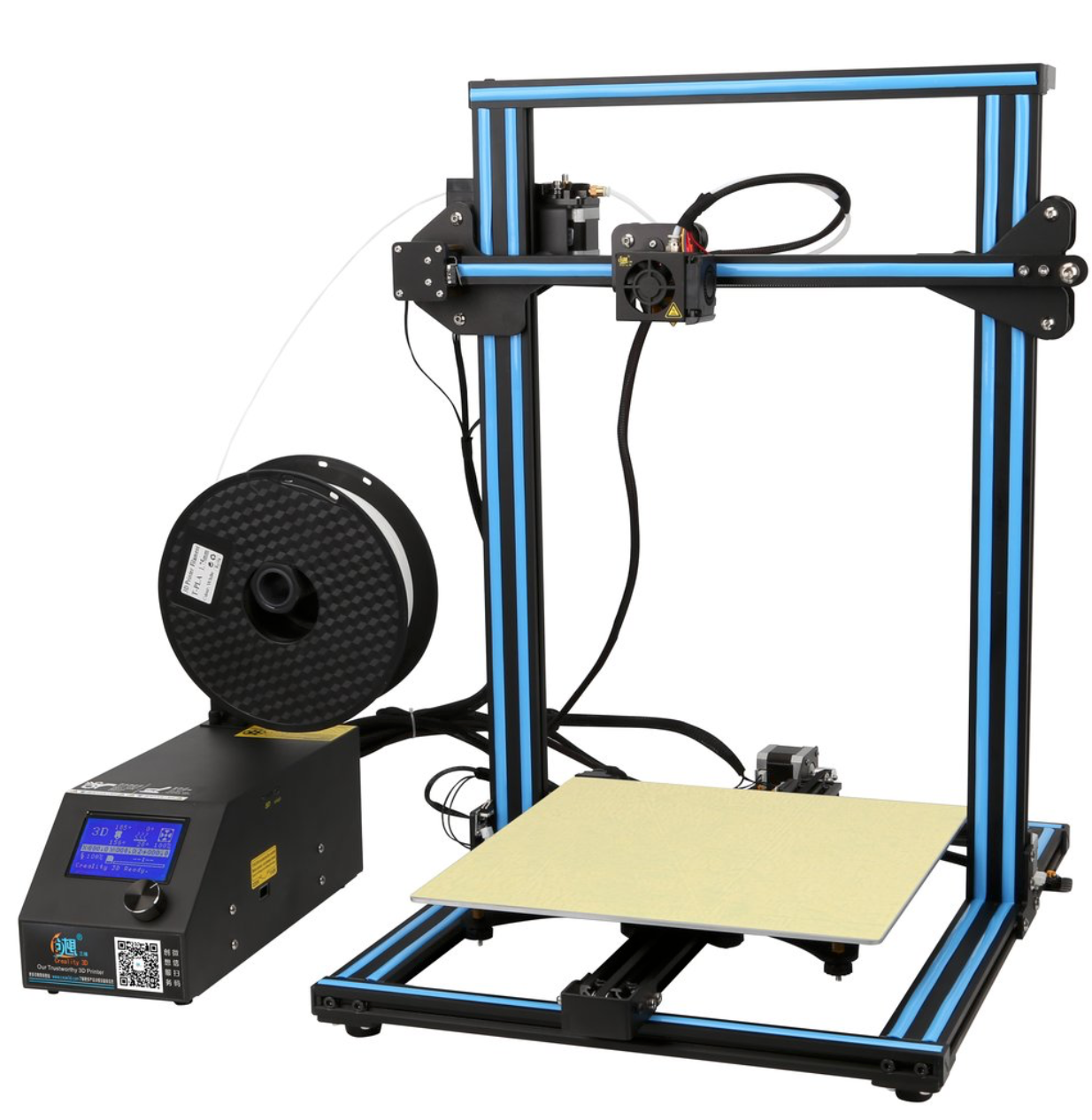
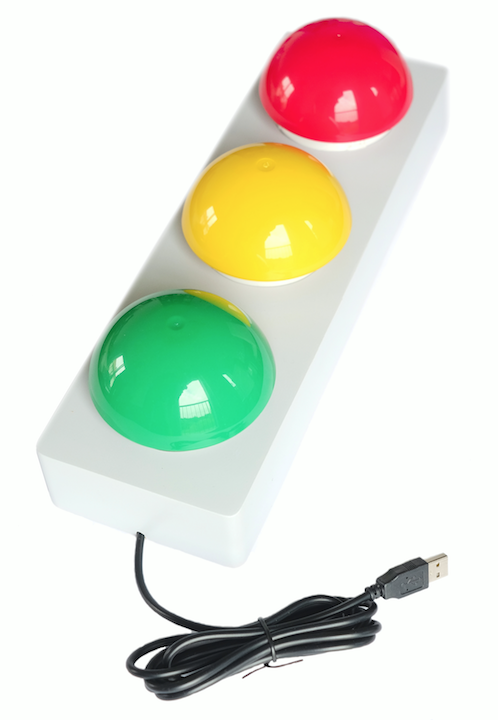
AR Viewer / eDrawings
Often we want to quickly see how an object with respective dimensions and shape would integrate into a specific environment. For example what it would look like to have an innovative new beverage dispenser on the kitchen unit. There are several ways to achieve this. We could take a photo of the real kitchen setting, create a photo realistic rendering of the object and photoshop it into the kitchen setting in order to get a 2D picture. Another way is to take the 3D CAD model and and an AR tool to project it onto the live kitchen setting. This enables us to shift perspective and look at the object in the kitchen setting from different angles. Smartphones and tablets can achieve good results with low-detail models. A higher level of detail (e.g. photo-realistic surfaces of an object) require high computing power that mobile devices cannot provide yet today. Especially for internal use a low-detail model and an AR tool are sufficient in most cases and easy to handle.
3. Q & A
We have no idea - which material shall we choose to build a haptic model? It depends on what you want to test and what kind of product it is. If surface texture is not important and its more about ergonomics or design aspects, hard foam is easy and fast for modeling. If prototypes need to withstand physical stress, if high functionality and/or if surface texture is important, then 3D-printing and finishing is a good choice.
Where can I get hard foam? Hard foam is usually sold in hardware stores in yellow or green blanks. It is much sturdier and more dense than normal white Styrofoam® and is usually available in a thickness of 20,40, and 60 mm.
We would like to do 3D printing but we are no CAD pros - how shall we start? Get someone who knows CAD. Otherwise it will take some time and a certain amount frustration tolerance learning how to design with a CAD tool. Ask our prototyping experts to help you!
Shall we already invest in a product designer? This depends on what the project is about. If high-quality visual sketches or if product design itself plays a major role right in the beginning, get a product designer. In a business design context and especially in the beginning, prototypes often don't have to be on a high visual or product design level yet. On the other side experienced product designers can give valuable advice or ideas at an early stage.
Do we need CAD designs if all we need is a high quality photorealistic rendering? Renderings need a digital surface structure which is then defined with textures, colors, reflections and shadows to look real. The digital surface structure can either be designed in a parametric CAD software (e.g. FreeCAD) or in a rendering software itself (e.g. Blender). Parametric CAD is better for precise technical and symmetrical shapes while rendering softwares are good for quick sketching of shapes which don't need to have exact measurements or which are rather organic.